Billet Shape Measurement and Quality Cut-to-Length System
Overview
The system realizes the fixed-length measurement of the width, thickness and length of the continuously cast product through machine vision and laser rangefinding system. The measured data is transmitted to the host system through the optical fiber. The host system calculates the weight of each billet according to different steel grades and specific gravity, so that we can realize the fixed length measurement and fixed weight control of the cast products and the precise control of the steelmaking process in the production process.
The slab number (automatic checking) can also be automatically identified online by using machine vision, and the weight and slab number can be automatically stored in the local database for use in the production and management system.
The measuring principle of the system
On the upper surface of the billet, a set of linear CCD cameras and a laser rangefinding instrument are respectively installed. Through machine vision and laser correction, we can achieve precise measurement of the cast products' shape. Through accurate cast products' shape monitoring, the billet thermal expansion coefficient of cast products and cast products' density at the current temperature, we can obtain the quality of the billet. At the same time, we can achieve high-precision quality cut-to-length , namely, fixed-weight and fixed-length.
The features of the equipment
The cutting control technology for fixed-length and fixed-weight of cast products is a concrete manifestation of the lean production management of steel products. In the era of high-quality competition of steel products, only high-end intelligent technology and management can reduce costs, improve quality and market competitiveness.
1. Data management can be carried out according to shifts, pouring times, days, weeks, months, etc., as well as data management according to specifications, production capacity, quality, etc.
2. Each stream can send out signals such as pre-clamping, clamping, cutting, roll-up, roll-down and return of the cutting car according to the user's requirements.
3. The detection and cutting precision is high, the controllable length sizing accuracy is ±1mm, and the quality sizing accuracy is more than 1.5‰.
4. It is not sensitive to other high-intensity light interference, and overcomes the influence of light sources such as sunlight and arc welding.
5. The monitor displays the running status of the current hot billet in real time and displays the corresponding parameters.
6. Laser rangefinding and CCD machine vision are used to calculate the weight of the cast products and optimize the cutting to length.
7. Historical cutting data is automatically stored, and the system can set rules for historical data.
8. Support the free transformation of fixed length, and a variety of operation modes are available for the operator to choose.
9. Adopt advanced high temperature laser measurement and high pixel linear CCD technology.
10. The system provides abundant interfaces, which can communicate with the PLC control.
11. Applicable to all kinds of continuous casting machine flame cutting system.
12. Provide automatic, upper and manual cutting control.
The main technical requirements
1. Width range of the inspected cast product: 120~2000 mm
2. Length range of the inspected cast product: 1000~20000 mm
3. Thickness range of the inspected cast product: 35~400 mm
4. Steel plate moving speed: < 3.5 m/s
5. Temperature of the measured steel plate: 0~850 °C
6. Measurement accuracy: width ±0.5mm
Thickness ±0.2mm
Length ±0.2mm
7. Weight calculation accuracy: 1.2‰ (temperature model verification)
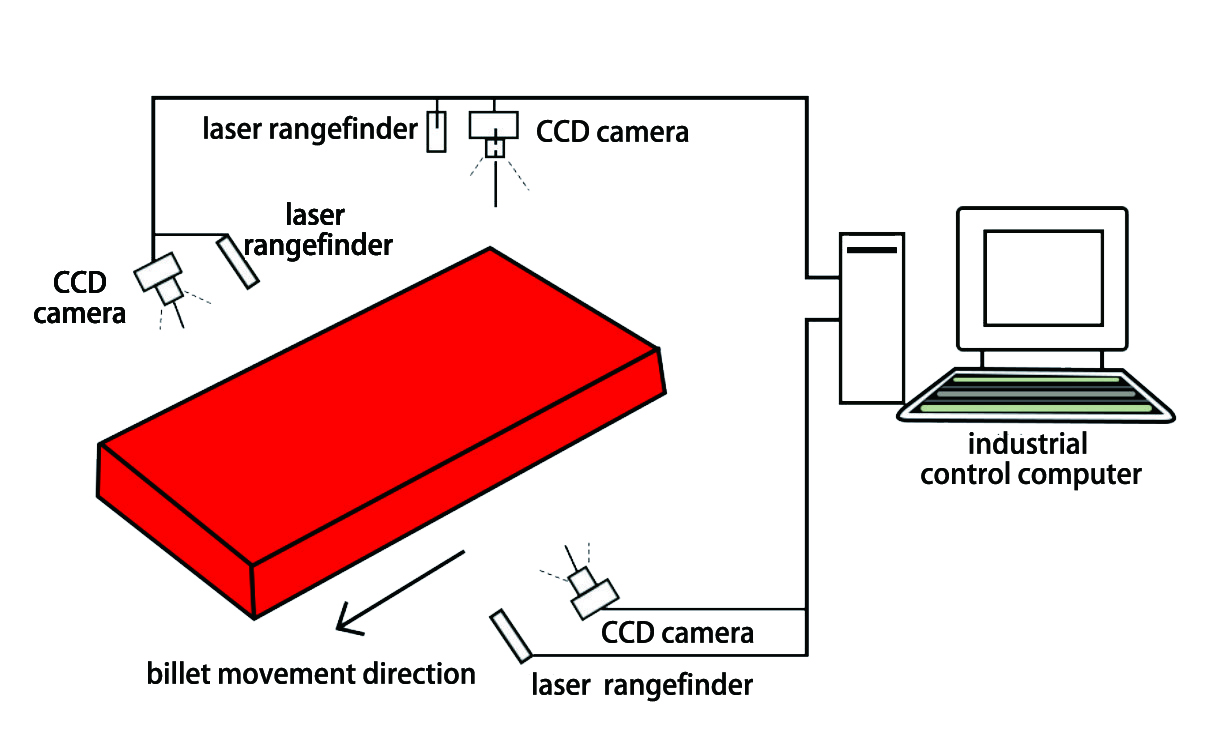
Location : Hengxin Industrial Park,Wuhu, Huangpi, Wuhan, Hubei, China, 432200 Wuhan,
Contact : Floria Liang, 8613995588597